Advantages And Applications Of Spiral Welded Tubes In Modern Industry
Introduce:
In the ever-growing fields of engineering and construction, the use of spiral welded pipe is becoming increasingly popular. These flexible and durable pipes have made their way into various industries, proving to be a revolutionary solution for a variety of applications. In this blog post, we’ll take a closer look at the incredible advantages offered by spiral welded pipes and explore their diverse applications in modern industry.
Mechanical Property
steel grade |
minimum yield strength |
Tensile strength |
Minimum elongation |
Minimum impact energy |
||||
Specified thickness |
Specified thickness |
Specified thickness |
at test temperature of |
|||||
<16 |
>16≤40 |
<3 |
≥3≤40 |
≤40 |
-20℃ |
0℃ |
20℃ |
|
S235JRH |
235 |
225 |
360-510 |
360-510 |
24 |
- |
- |
27 |
S275J0H |
275 |
265 |
430-580 |
410-560 |
20 |
- |
27 |
- |
S275J2H |
27 |
- |
- |
|||||
S355J0H |
365 |
345 |
510-680 |
470-630 |
20 |
- |
27 |
- |
S355J2H |
27 |
- |
- |
|||||
S355K2H |
40 |
- |
- |
1. What is spiral welded pipe?
Spiral welded tube, as the name suggests, is manufactured by continuously rolling steel strip and welding it along its length to form a spiral pipe. This manufacturing technique ensures superior strength and integrity, making these tubes ideal for demanding applications.
2. Advantages of spiral welded pipe:
2.1 Strength and durability:
The spiral welding process inherently gives the pipe superior strength. This allows them to withstand high internal pressures, heavy loads and extreme temperatures. Therefore, they are widely used in industries where structural integrity is critical.
2.2 Corrosion resistance:
Spiral welded pipe is available in a variety of materials, including stainless steel and corrosion-resistant alloys. Their corrosion resistance makes them ideal for applications in the chemical, oil and gas, and water treatment industries. They extend service life and reduce the risk of leaks and downtime.
2.3 Cost-effectiveness:
Spiral welding offers cost advantages compared to traditional pipe manufacturing methods. This is due to reduced production time and reduced material consumption. In addition, the excellent formability of spiral welded pipes allows for custom designs and customized solutions, further optimizing costs by reducing waste and minimizing the need for additional accessories.
3. Application of spiral welded pipe:
3.1 Buildings and Infrastructure:
Spiral welded pipes are widely used in the construction industry, especially in large-scale projects. They are commonly used to create column, beam and pile structures. Due to its high strength, it can withstand heavy loads and resist lateral forces, making it suitable for bridge construction, high-rise buildings and deep foundations.
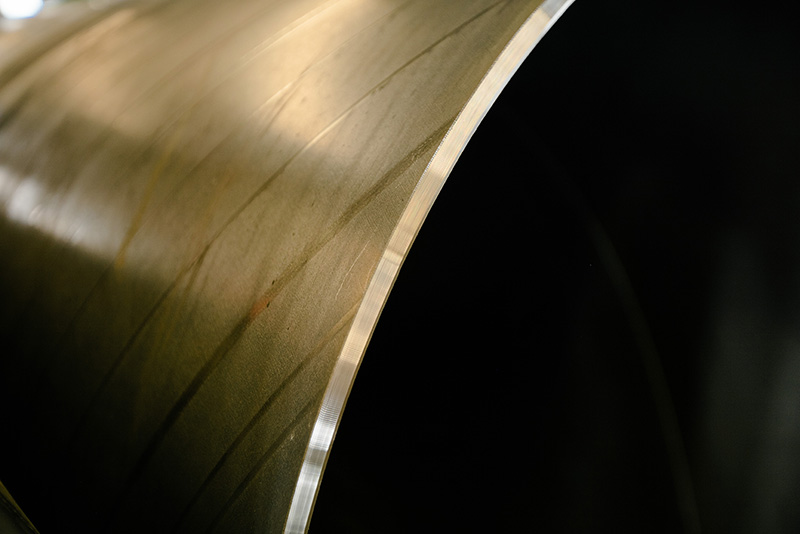
3.2 Oil and gas industry:
In the oil and gas sector, spiral welded pipes are widely used for the transportation of petroleum products, natural gas and other fluids. The pipe's ability to withstand high-pressure environments, suitability for deep-sea applications and corrosion resistance make it the first choice for pipelines, risers and offshore installations.
3.3 Mechanical Engineering:
Spiral welded pipes are used in a wide range of applications in mechanical engineering and stand out for their durability and versatility. They are used in the manufacture of machinery, transport systems and structural components. Additionally, they play a vital role in the automotive industry, providing overall structural support to the frame and exhaust system.
In conclusion:
As the industry continues to evolve, the need for robust, durable and cost-effective solutions continues to grow. Spiral welded pipes successfully meet these needs and become an indispensable asset in many fields. Their superior strength, corrosion resistance and cost-effectiveness further solidify their position as the first choice for a variety of engineering applications. As we move forward, it’s clear that spiral welded pipe will continue to shape the future of modern industry.
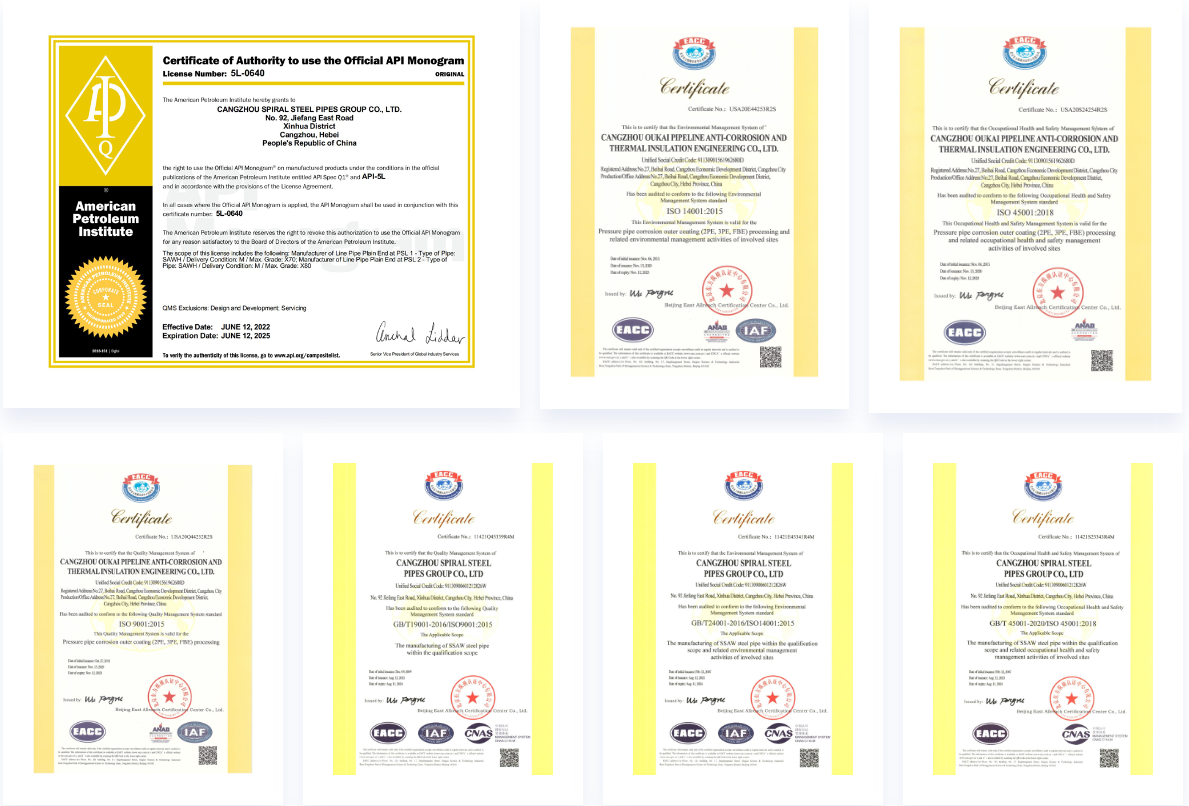