Hollow-Section Structural Pipes For Underground Natural Gas Lines
Spiral submerged arc pipes are widely used in the construction of underground natural gas lines due to their unique manufacturing process. The pipes are formed by forming coils of hot-rolled steel into a spiral shape and then welding them using a submerged arc welding process. This produces high-strength Spiral submerged arc pipes with uniform thickness and excellent dimensional accuracy, making them ideal for underground natural gas transportation.
Table 2 Main Physical and Chemical Properties of Steel Pipes (GB/T3091-2008, GB/T9711-2011 and API Spec 5L) |
||||||||||||||
Standard |
Steel Grade |
Chemical Constituents (%) |
Tensile Property |
Charpy(V notch)Impact Test |
||||||||||
c | Mn | p | s | Si |
Other |
Yield Strength(Mpa) |
Tensile Strength(Mpa) |
(L0=5.65 √ S0 )min Stretch Rate (%) |
||||||
max | max | max | max | max | min | max | min | max | D ≤ 168.33mm | D > 168.3mm | ||||
GB/T3091 -2008 |
Q215A | ≤ 0.15 | 0.25 < 1.20 | 0.045 | 0.050 | 0.35 |
Adding Nb\V\Ti in accordance with GB/T1591-94 |
215 |
|
335 |
|
15 | > 31 |
|
Q215B | ≤ 0.15 | 0.25-0.55 | 0.045 | 0.045 | 0.035 | 215 | 335 | 15 | > 31 | |||||
Q235A | ≤ 0.22 | 0.30 < 0.65 | 0.045 | 0.050 | 0.035 | 235 | 375 | 15 | >26 | |||||
Q235B | ≤ 0.20 | 0.30 ≤ 1.80 | 0.045 | 0.045 | 0.035 | 235 | 375 | 15 | >26 | |||||
Q295A | 0.16 | 0.80-1.50 | 0.045 | 0.045 | 0.55 | 295 | 390 | 13 | >23 | |||||
Q295B | 0.16 | 0.80-1.50 | 0.045 | 0.040 | 0.55 | 295 | 390 | 13 | >23 | |||||
Q345A | 0.20 | 1.00-1.60 | 0.045 | 0.045 | 0.55 | 345 | 510 | 13 | >21 | |||||
Q345B | 0.20 | 1.00-1.60 | 0.045 | 0.040 | 0.55 | 345 | 510 | 13 | >21 | |||||
GB/T9711-2011(PSL1) |
L175 | 0.21 | 0.60 | 0.030 | 0.030 |
|
Optional adding one of Nb\V\Ti elements or any combination of them |
175 |
|
310 |
|
27 |
One or two of the toughness index of impact energy and shearing area may be chosen. For L555, see the standard. |
|
L210 | 0.22 | 0.90 | 0.030 | 0.030 | 210 | 335 |
25 |
|||||||
L245 | 0.26 | 1.20 | 0.030 | 0.030 | 245 | 415 |
21 |
|||||||
L290 | 0.26 | 1.30 | 0.030 | 0.030 | 290 | 415 |
21 |
|||||||
L320 | 0.26 | 1.40 | 0.030 | 0.030 | 320 | 435 |
20 |
|||||||
L360 | 0.26 | 1.40 | 0.030 | 0.030 | 360 | 460 |
19 |
|||||||
L390 | 0.26 | 1.40 | 0.030 | 0.030 | 390 | 390 |
18 |
|||||||
L415 | 0.26 | 1.40 | 0.030 | 0.030 | 415 | 520 |
17 |
|||||||
L450 | 0.26 | 1.45 | 0.030 | 0.030 | 450 | 535 |
17 |
|||||||
L485 | 0.26 | 1.65 | 0.030 | 0.030 | 485 | 570 |
16 |
|||||||
API 5L (PSL 1) |
A25 | 0.21 | 0.60 | 0.030 | 0.030 |
|
For grade B steel,Nb+V ≤ 0.03%;for steel ≥ grade B,optional adding Nb or V or their combination, and Nb+V+Ti ≤ 0.15% |
172 |
|
310 |
|
(L0=50.8mm)to be calculated according to the following formula:e=1944·A0 .2/U0 .0 A:Area of sample in mm2 U: Minimal specified tensile strength in Mpa |
None or any or both of the impact energy and the shearing area is required as toughness criterion. |
|
A | 0.22 | 0.90 | 0.030 | 0.030 |
|
207 | 331 | |||||||
B | 0.26 | 1.20 | 0.030 | 0.030 |
|
241 | 414 | |||||||
X42 | 0.26 | 1.30 | 0.030 | 0.030 |
|
290 | 414 | |||||||
X46 | 0.26 | 1.40 | 0.030 | 0.030 |
|
317 | 434 | |||||||
X52 | 0.26 | 1.40 | 0.030 | 0.030 |
|
359 | 455 | |||||||
X56 | 0.26 | 1.40 | 0.030 | 0.030 |
|
386 | 490 | |||||||
X60 | 0.26 | 1.40 | 0.030 | 0.030 |
|
414 | 517 | |||||||
X65 | 0.26 | 1.45 | 0.030 | 0.030 |
|
448 | 531 | |||||||
X70 | 0.26 | 1.65 | 0.030 | 0.030 |
|
483 | 565 |
One of the main advantages of hollow-section structural pipes is their excellent corrosion resistance. When buried underground, natural gas pipelines are exposed to moisture, soil chemicals and other corrosive elements. Spiral submerged arc pipes are specifically designed to withstand these harsh underground conditions, ensuring the longevity and reliability of natural gas pipelines.
In addition to corrosion resistance, hollow-section structural pipes offer superior strength and stability, making them suitable for underground installations. The spiral design of these pipes provides excellent load-bearing capacity, allowing them to withstand the weight of soil and other external forces without compromising their structural integrity. This is particularly important in areas with challenging geology, where pipelines must be able to withstand ground movement and settlement.
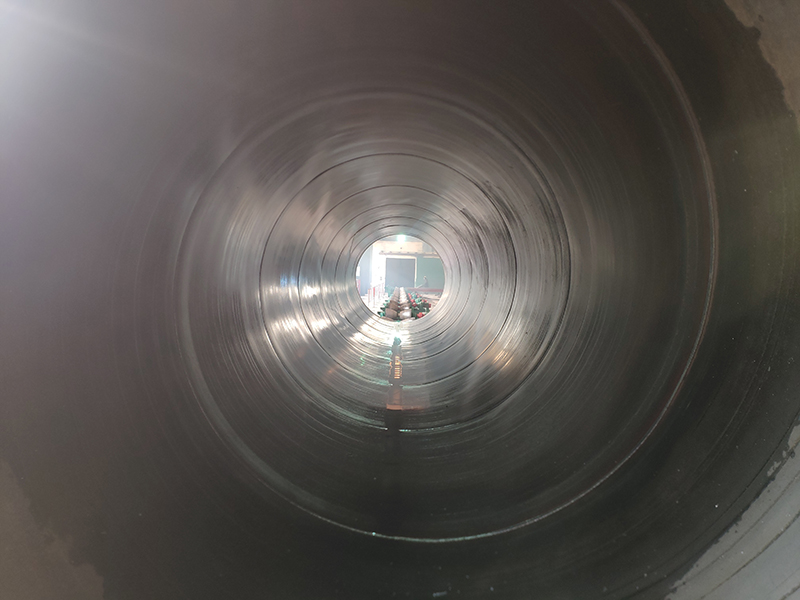
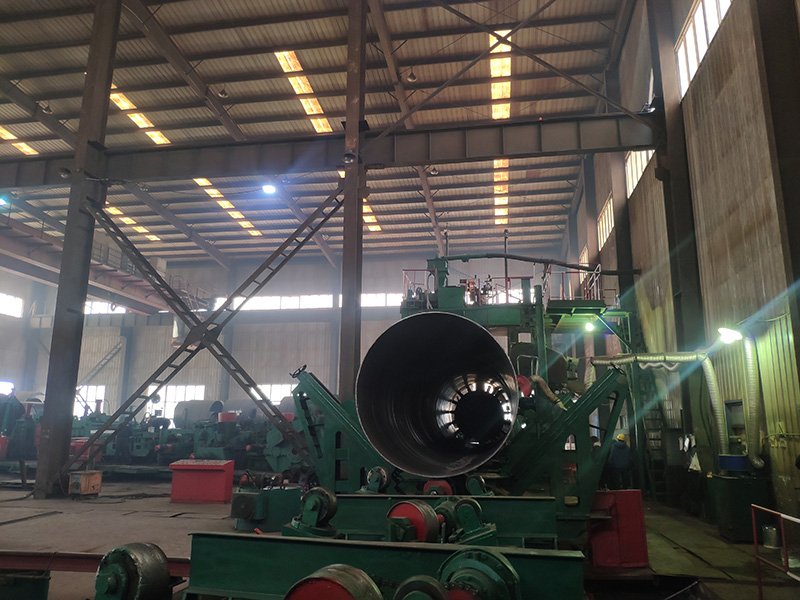
Additionally, hollow section structural pipes are known for their versatility and cost-effectiveness. They come in a wide range of sizes and thicknesses and can be customized to meet the specific requirements of underground natural gas pipeline projects. This in turn reduces the need for additional fittings and welding, resulting in faster installation and lower overall costs. The lightweight nature of these pipes also makes transportation and handling more efficient, further contributing to cost savings.
When it comes to the safety and efficiency of underground natural gas lines, material selection is critical. Hollow-section structural pipes, especially spiral submerged arc pipes, combine strength, durability, corrosion resistance and cost-effectiveness, making them ideal for underground natural gas transmission. By investing in high-quality pipelines designed specifically for underground facilities, gas companies can ensure the reliability and longevity of their infrastructure while minimizing maintenance and repair costs in the long term.
In summary, hollow cross-section structural pipes play a vital role in the construction of underground natural gas lines. Its superior corrosion resistance, superior strength and cost-effectiveness make it the first choice for natural gas transportation projects. By choosing the right materials for underground facilities, natural gas companies can maintain the safety and reliability of their infrastructure, ultimately helping to deliver natural gas efficiently to consumers.
