In the world of industrial piping, the choice of materials and construction methods can significantly impact the efficiency and durability of the project. One such innovative solution is the spiral seam welded pipe, which is popular in various fields due to its unique manufacturing process and numerous advantages. In this blog, we will explore what spiral seam welded pipes are, their applications and the benefits they bring.
What is spiral seam welded pipe?
Spiral seam welded pipe is made by rolling flat steel strip into a spiral shape and then welding the edges together. This construction method allows the creation of pipes with larger diameters and thinner walls than traditional straight seam welded pipes. The spiral welding process involves a continuous feed of steel strips that are formed into a spiral and welded in one go, resulting in a strong and durable product.
Application of spiral seam welded pipe
Spiral seam welded pipe is versatile and can be used for a variety of purposes, including:
1. Oil and Gas Industry: These pipelines are commonly used to transport oil and gas because of their ability to withstand high pressures and corrosive environments. Their larger diameter makes them ideal for transporting over long distances.
2. Water supply and sewage treatment systems: The durability and corrosion resistance of spiral seam welded pipes make them suitable for water supply systems and sewage pipes. They can withstand the pressure and flow required by municipal water systems.
3. Construction and Infrastructure: In construction, these pipes are often used for piling and foundation works. Their strength and stability make them an excellent choice for supporting structures.
4. Agricultural Applications: Spiral seam welded pipes are also used in irrigation systems to effectively transport water to crops over long distances.
5. Industrial Applications: Various industries utilize these pipes to transport chemicals, slurries, and other materials that require robust piping solutions.
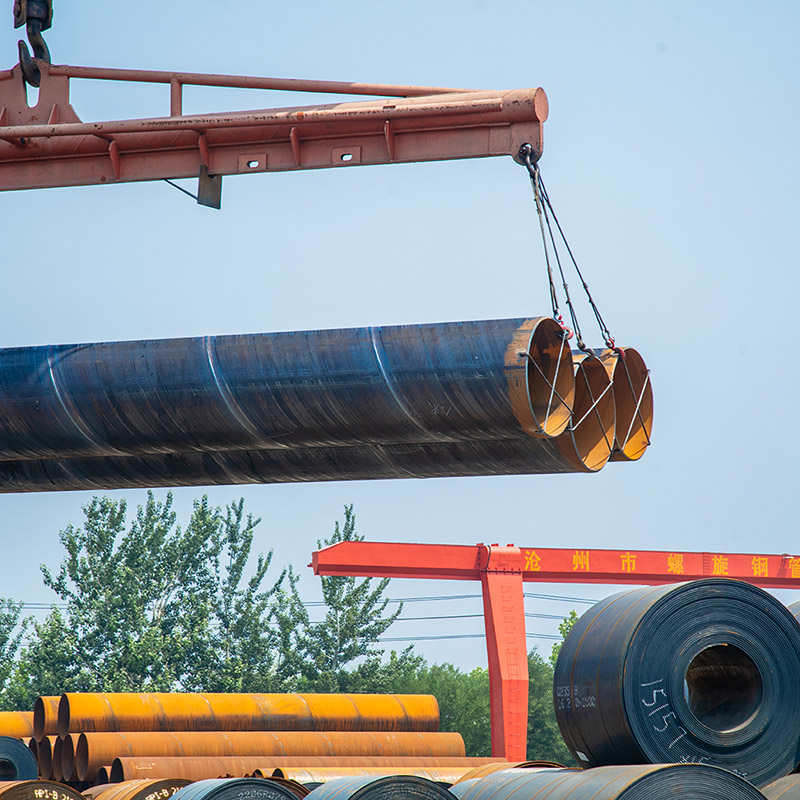
Advantages of spiral seam welded pipe
Spiral seam welded pipe offers several advantages that make it the first choice in many applications:
1. Cost Effectiveness: The manufacturing process for spiral seam welded pipe is generally more economical than other types of pipe. The ability to produce larger diameter, thinner wall pipes reduces material costs while maintaining strength.
2. High Strength to Weight Ratio: Spiral welding technology allows for a high strength to weight ratio, making these pipes easier to handle and install without compromising structural integrity.
3. Design Flexibility: The manufacturing process allows for customization in diameter, wall thickness, and length, making it easier to meet specific project requirements.
4. Corrosion Resistance: Many spiral seam welded pipes are coated or treated to enhance their corrosion resistance, extend their service life and reduce maintenance costs.
5. Seamless Flow: The spiral design minimizes turbulence and allows fluids to flow more smoothly, which is especially beneficial in applications involving liquid transportation.
In conclusion
Spiral seam welded pipe represents a significant advancement in pipe technology, combining strength, durability and cost-effectiveness. Their versatility makes them suitable for applications ranging from oil and gas transportation to agricultural irrigation. As industries continue to seek efficient and reliable piping solutions, the popularity of spiral seam welded pipes is likely to continue to grow, cementing its position as a key component of modern infrastructure. Whether you are involved in construction, energy or water management, understanding the benefits of spiral seam welded pipe can help you make informed decisions for your project.
Post time: Dec-09-2024