Spiral Submerged Arc Welded Pipes For Modern Industry
Advantages of spiral submerged arc welded pipe:
1. Efficient construction:
SSAW pipes feature a spiral weld design that allows for efficient production and reduced manufacturing time. This unique characteristic makes it the first choice for large-scale construction projects such as oil and gas pipes, water transmission systems, and offshore drilling platforms. The continuous welding process ensures a high degree of structural integrity, increasing the durability and service life of the pipe.
Standard |
Steel grade |
Chemical composition |
Tensile properties |
Charpy Impact Test and Drop Weight Tear Test |
||||||||||||||
C | Si | Mn | P | S | V | Nb | Ti | CEV4)(%) | Rt0.5 Mpa Yield strength | Rm Mpa Tensile Strength | Rt0.5/ Rm | (L0=5.65 √ S0 )Elongation A% | ||||||
max | max | max | max | max | max | max | max | Other | max | min | max | min | max | max | min | |||
L245MB |
0.22 |
0.45 |
1.2 |
0.025 |
0.15 |
0.05 |
0.05 |
0.04 |
1) |
0.4 |
245 |
450 |
415 |
760 |
0.93 |
22 |
Charpy impact test: Impact absorbing energy of pipe body and weld seam shall be tested as required in the original standard. For details, see the original standard. Drop weight tear test: Optional shearing area |
|
GB/T9711-2011(PSL2) |
L290MB |
0.22 |
0.45 |
1.3 |
0.025 |
0.015 |
0.05 |
0.05 |
0.04 |
1) |
0.4 |
290 |
495 |
415 |
21 |
|||
L320MB |
0.22 |
0.45 |
1.3 |
0.025 |
0.015 |
0.05 |
0.05 |
0.04 |
1) |
0.41 |
320 |
500 |
430 |
21 |
||||
L360MB |
0.22 |
0.45 |
1.4 |
0.025 |
0.015 |
1) |
0.41 |
360 |
530 |
460 |
20 |
|||||||
L390MB |
0.22 |
0.45 |
1.4 |
0.025 |
0.15 |
1) |
0.41 |
390 |
545 |
490 |
20 |
|||||||
L415MB |
0.12 |
0.45 |
1.6 |
0.025 |
0.015 |
1)2)3 |
0.42 |
415 |
565 |
520 |
18 |
|||||||
L450MB |
0.12 |
0.45 |
1.6 |
0.025 |
0.015 |
1)2)3 |
0.43 |
450 |
600 |
535 |
18 |
|||||||
L485MB |
0.12 |
0.45 |
1.7 |
0.025 |
0.015 |
1)2)3 |
0.43 |
485 |
635 |
570 |
18 |
|||||||
L555MB |
0.12 |
0.45 |
1.85 |
0.025 |
0.015 |
1)2)3 | Negotiation |
555 |
705 |
625 |
825 |
0.95 |
18 |
2. Excellent strength and flexibility:
The spiral structure of SSAW pipe increases its strength, allowing it to resist external and internal pressures. These pipes are able to withstand extreme atmospheric conditions, making them suitable for above and below ground applications. Additionally, the flexibility of SSAW pipes allows them to be easily adapted and installed in a variety of terrains, including rough terrain and unstable soils.
3. Cost-effective solution:
Continuous welding processes increase productivity while significantly reducing welding defects and costs. Additionally, spiral submerged arc welded pipes offer superior strength and durability, reducing maintenance and repair costs over their lifetime, making them an economical choice for industry.
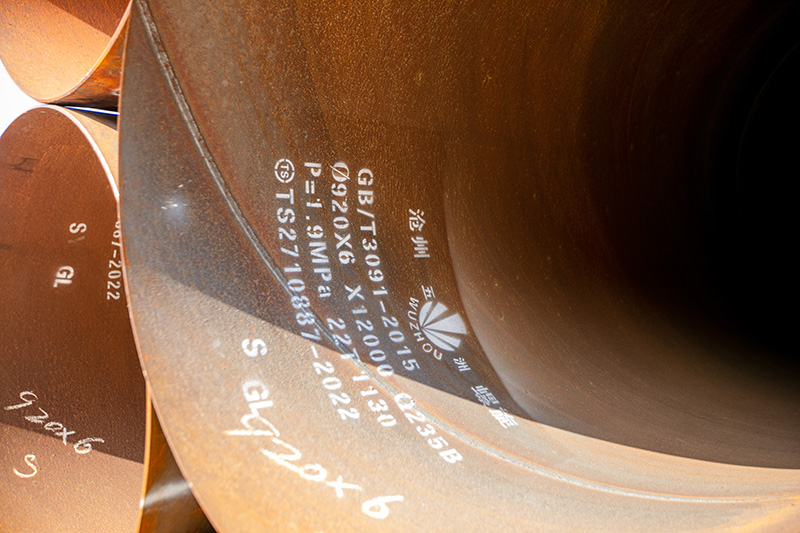
Challenges faced by spiral submerged arc welded pipes:
1. Quality control:
Because of the complex welding processes involved in producing spiral submerged arc welded pipes, ensuring consistent quality is challenging. If welding parameters are not controlled accurately, welding defects such as undercuts, pores, and lack of fusion will occur. To overcome this challenge, strict quality control measures and advanced monitoring systems during the manufacturing process are crucial.
2. Pipe diameter restriction range:
While spiral submerged arc welded pipes are ideal for large diameter applications, they may not be suitable for industries requiring smaller pipe sizes. The manufacturing process is more efficient for larger diameter pipes, resulting in limited availability for smaller projects such as residential piping and small industrial uses. For such requirements, alternative pipe manufacturing technologies should be considered.
3. Surface coating:
Another challenge facing the SSAW pipe industry is ensuring appropriate and durable surface coatings to protect against corrosion and wear. Coating application on spiral surfaces requires advanced equipment and expertise to ensure even coverage and adhesion. Proper surface coating is critical to extending the service life of spiral submerged arc welded pipe, especially in harsh environments.
In conclusion:
Spiral submerged arc welded pipes have proven to be a highly advantageous technology in modern industry, offering efficiency, strength and cost-effectiveness. Its unique spiral weld seam allows for efficient production and increased durability, making it suitable for large construction projects. However, for continued success and widespread adoption of this manufacturing technology, challenges such as quality control, limited diameter range, and surface coatings need to be addressed. By overcoming these challenges through technological advancement and industry collaboration, spiral submerged arc welded pipe has a promising future in transforming and sustaining critical infrastructure around the world.