Spiral Welded Steel Pipe For Oil And Gas Pipelines
Introduce:
In the ever-evolving fields of architecture and engineering, technological advancements continue to redefine how projects are implemented. One of the remarkable innovations is the spiral welded steel pipe. The pipe has seams on its surface and is created by bending steel strips into circles and then welding them, bringing exceptional strength, durability and versatility to the pipe welding process. This product introduction aims to illustrate the salient features of spiral welded pipe and highlight its transformative role in the oil and gas industry.
Product Description:
Spiral welded steel pipes, by their design, offer several distinct advantages over conventional piping systems. Its unique manufacturing process ensures a consistent thickness throughout its entire length, making it highly resistant to internal and external pressures. This robustness makes spiral welded pipe ideal for oil and gas transmission applications where safety and reliability are paramount.
The spiral welding technology used in its production provides greater flexibility and adaptability, allowing the pipeline to withstand extreme conditions such as high temperatures, pressure differences and natural disasters. In addition, this innovative design enhances corrosion and wear resistance, helping to extend service life and reduce maintenance costs.
Table 2 Main Physical and Chemical Properties of Steel Pipes (GB/T3091-2008, GB/T9711-2011 and API Spec 5L) | ||||||||||||||
Standard | Steel Grade | Chemical Constituents (%) | Tensile Property | Charpy(V notch)Impact Test | ||||||||||
c | Mn | p | s | Si | Other | Yield Strength(Mpa) | Tensile Strength(Mpa) | (L0=5.65 √ S0 )min Stretch Rate (%) | ||||||
max | max | max | max | max | min | max | min | max | D ≤ 168.33mm | D > 168.3mm | ||||
GB/T3091 -2008 | Q215A | ≤ 0.15 | 0.25 < 1.20 | 0.045 | 0.050 | 0.35 | Adding Nb\V\Ti in accordance with GB/T1591-94 | 215 | 335 | 15 | > 31 | |||
Q215B | ≤ 0.15 | 0.25-0.55 | 0.045 | 0.045 | 0.035 | 215 | 335 | 15 | > 31 | |||||
Q235A | ≤ 0.22 | 0.30 < 0.65 | 0.045 | 0.050 | 0.035 | 235 | 375 | 15 | >26 | |||||
Q235B | ≤ 0.20 | 0.30 ≤ 1.80 | 0.045 | 0.045 | 0.035 | 235 | 375 | 15 | >26 | |||||
Q295A | 0.16 | 0.80-1.50 | 0.045 | 0.045 | 0.55 | 295 | 390 | 13 | >23 | |||||
Q295B | 0.16 | 0.80-1.50 | 0.045 | 0.040 | 0.55 | 295 | 390 | 13 | >23 | |||||
Q345A | 0.20 | 1.00-1.60 | 0.045 | 0.045 | 0.55 | 345 | 510 | 13 | >21 | |||||
Q345B | 0.20 | 1.00-1.60 | 0.045 | 0.040 | 0.55 | 345 | 510 | 13 | >21 | |||||
GB/T9711-2011(PSL1) | L175 | 0.21 | 0.60 | 0.030 | 0.030 | Optional adding one of Nb\V\Ti elements or any combination of them | 175 | 310 | 27 | One or two of the toughness index of impact energy and shearing area may be chosen. For L555, see the standard. | ||||
L210 | 0.22 | 0.90 | 0.030 | 0.030 | 210 | 335 | 25 | |||||||
L245 | 0.26 | 1.20 | 0.030 | 0.030 | 245 | 415 | 21 | |||||||
L290 | 0.26 | 1.30 | 0.030 | 0.030 | 290 | 415 | 21 | |||||||
L320 | 0.26 | 1.40 | 0.030 | 0.030 | 320 | 435 | 20 | |||||||
L360 | 0.26 | 1.40 | 0.030 | 0.030 | 360 | 460 | 19 | |||||||
L390 | 0.26 | 1.40 | 0.030 | 0.030 | 390 | 390 | 18 | |||||||
L415 | 0.26 | 1.40 | 0.030 | 0.030 | 415 | 520 | 17 | |||||||
L450 | 0.26 | 1.45 | 0.030 | 0.030 | 450 | 535 | 17 | |||||||
L485 | 0.26 | 1.65 | 0.030 | 0.030 | 485 | 570 | 16 | |||||||
API 5L (PSL 1) | A25 | 0.21 | 0.60 | 0.030 | 0.030 | For grade B steel,Nb+V ≤ 0.03%;for steel ≥ grade B,optional adding Nb or V or their combination, and Nb+V+Ti ≤ 0.15% | 172 | 310 | (L0=50.8mm)to be calculated according to the following formula:e=1944·A0 .2/U0 .0 A:Area of sample in mm2 U: Minimal specified tensile strength in Mpa | None or any or both of the impact energy and the shearing area is required as toughness criterion. | ||||
A | 0.22 | 0.90 | 0.030 | 0.030 | 207 | 331 | ||||||||
B | 0.26 | 1.20 | 0.030 | 0.030 | 241 | 414 | ||||||||
X42 | 0.26 | 1.30 | 0.030 | 0.030 | 290 | 414 | ||||||||
X46 | 0.26 | 1.40 | 0.030 | 0.030 | 317 | 434 | ||||||||
X52 | 0.26 | 1.40 | 0.030 | 0.030 | 359 | 455 | ||||||||
X56 | 0.26 | 1.40 | 0.030 | 0.030 | 386 | 490 | ||||||||
X60 | 0.26 | 1.40 | 0.030 | 0.030 | 414 | 517 | ||||||||
X65 | 0.26 | 1.45 | 0.030 | 0.030 | 448 | 531 | ||||||||
X70 | 0.26 | 1.65 | 0.030 | 0.030 | 483 | 565 |
In addition, the connection of the spiral weld ensures excellent leak-proof performance. Therefore, spiral welded pipes provide safe pipelines for oil and gas transportation, minimizing the risk of leaks and environmental hazards. This, coupled with its high flow efficiency and optimal hydraulic performance, makes it ideal for energy companies looking for reliable and sustainable solutions.
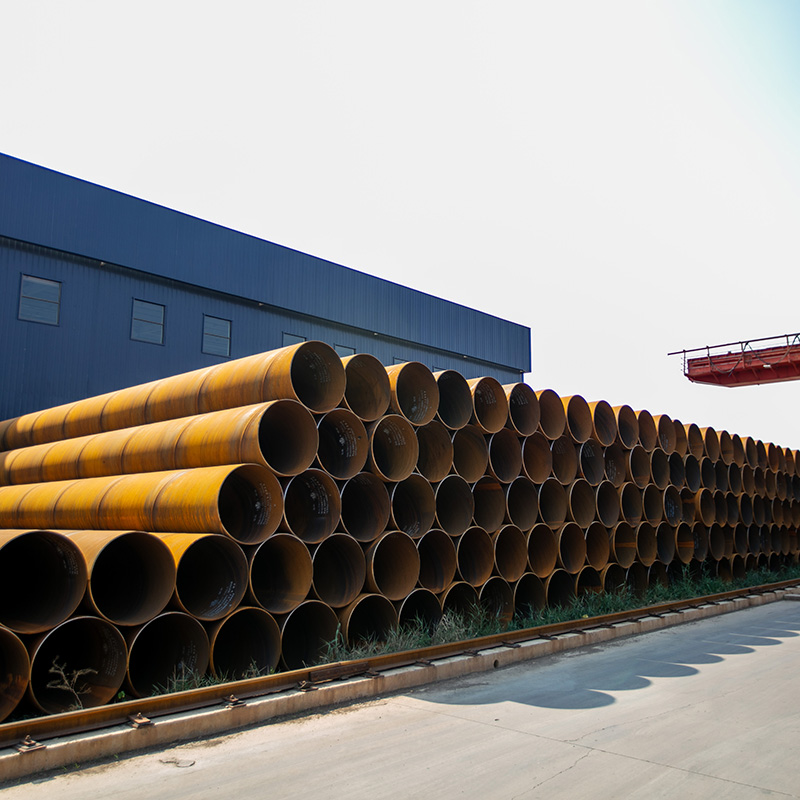
The versatility of spiral welded pipe is not limited to oil and gas transportation. Its strong construction and excellent structural integrity allow it to be used in a variety of applications, including water supply, drainage systems, and even civil engineering projects. Whether used to transport liquids or used as support structures, spiral welded steel pipes excel in providing reliable and cost-effective solutions.
The introduction of spiral welded steel pipes has significantly improved pipe welding procedures, simplifying the process and reducing overall project time. Easy installation, combined with a high strength-to-weight ratio, allows for a more streamlined and efficient construction process. This means significant savings in labor costs, equipment requirements and project management expenses, while ensuring superior quality and longevity.
In conclusion:
In summary, spiral welded pipe has revolutionized the field of pipe welding processes, especially in the oil and gas industry. Its seamless integration of strength, durability, versatility and cost-effectiveness make it ideal for energy companies looking for reliable solutions. With superior pressure, corrosion and leakage resistance, spiral welded steel pipes go beyond traditional pipeline systems to provide a sustainable and safe network for the transportation of vital resources. As the construction industry continues to embrace technological advancement, spiral welded pipe becomes a testament to human ingenuity and innovation, heralding a future of efficiency, safety and reliability.