Strength of Double Welded Pipe in Industrial Applications
Double welded pipes are constructed with two independent welds to form a strong and reliable connection between pipe sections. This double welding process ensures that the pipe can withstand the stresses and strains that may be encountered during operation, making it a reliable choice for critical applications where failure is not an option.
One of the main advantages of double-welded pipes is their ability to handle high-pressure environments. The double welding process creates a seamless and strong connection between the pipe sections, ensuring they can withstand internal pressures without the risk of leaks or failure. This makes them ideal for applications such as oil and gas pipelines, where the integrity of the pipeline system is critical to safety and operational efficiency.
Table 2 Main Physical and Chemical Properties of Steel Pipes (GB/T3091-2008, GB/T9711-2011 and API Spec 5L) |
||||||||||||||
Standard |
Steel Grade |
Chemical Constituents (%) |
Tensile Property |
Charpy(V notch)Impact Test |
||||||||||
c | Mn | p | s | Si |
Other |
Yield Strength(Mpa) |
Tensile Strength(Mpa) |
(L0=5.65 √ S0 )min Stretch Rate (%) |
||||||
max | max | max | max | max | min | max | min | max | D ≤ 168.33mm | D > 168.3mm | ||||
GB/T3091 -2008 |
Q215A | ≤ 0.15 | 0.25 < 1.20 | 0.045 | 0.050 | 0.35 |
Adding NbVTi in accordance with GB/T1591-94 |
215 |
|
335 |
|
15 | > 31 |
|
Q215B | ≤ 0.15 | 0.25-0.55 | 0.045 | 0.045 | 0.035 | 215 | 335 | 15 | > 31 | |||||
Q235A | ≤ 0.22 | 0.30 < 0.65 | 0.045 | 0.050 | 0.035 | 235 | 375 | 15 | >26 | |||||
Q235B | ≤ 0.20 | 0.30 ≤ 1.80 | 0.045 | 0.045 | 0.035 | 235 | 375 | 15 | >26 | |||||
Q295A | 0.16 | 0.80-1.50 | 0.045 | 0.045 | 0.55 | 295 | 390 | 13 | >23 | |||||
Q295B | 0.16 | 0.80-1.50 | 0.045 | 0.040 | 0.55 | 295 | 390 | 13 | >23 | |||||
Q345A | 0.20 | 1.00-1.60 | 0.045 | 0.045 | 0.55 | 345 | 510 | 13 | >21 | |||||
Q345B | 0.20 | 1.00-1.60 | 0.045 | 0.040 | 0.55 | 345 | 510 | 13 | >21 | |||||
GB/T9711-2011(PSL1) |
L175 | 0.21 | 0.60 | 0.030 | 0.030 |
|
Optional adding one of NbVTi elements or any combination of them |
175 |
|
310 |
|
27 |
One or two of the toughness index of impact energy and shearing area may be chosen. For L555, see the standard. |
|
L210 | 0.22 | 0.90 | 0.030 | 0.030 | 210 | 335 |
25 |
|||||||
L245 | 0.26 | 1.20 | 0.030 | 0.030 | 245 | 415 |
21 |
|||||||
L290 | 0.26 | 1.30 | 0.030 | 0.030 | 290 | 415 |
21 |
|||||||
L320 | 0.26 | 1.40 | 0.030 | 0.030 | 320 | 435 |
20 |
|||||||
L360 | 0.26 | 1.40 | 0.030 | 0.030 | 360 | 460 |
19 |
|||||||
L390 | 0.26 | 1.40 | 0.030 | 0.030 | 390 | 390 |
18 |
|||||||
L415 | 0.26 | 1.40 | 0.030 | 0.030 | 415 | 520 |
17 |
|||||||
L450 | 0.26 | 1.45 | 0.030 | 0.030 | 450 | 535 |
17 |
|||||||
L485 | 0.26 | 1.65 | 0.030 | 0.030 | 485 | 570 |
16 |
|||||||
API 5L (PSL 1) |
A25 | 0.21 | 0.60 | 0.030 | 0.030 |
|
For grade B steel,Nb+V ≤ 0.03%;for steel ≥ grade B,optional adding Nb or V or their combination, and Nb+V+Ti ≤ 0.15% |
172 |
|
310 |
|
(L0=50.8mm)to be calculated according to the following formula:e=1944·A0 .2/U0 .0 A:Area of sample in mm2 U: Minimal specified tensile strength in Mpa |
None or any or both of the impact energy and the shearing area is required as toughness criterion. |
|
A | 0.22 | 0.90 | 0.030 | 0.030 |
|
207 | 331 | |||||||
B | 0.26 | 1.20 | 0.030 | 0.030 |
|
241 | 414 | |||||||
X42 | 0.26 | 1.30 | 0.030 | 0.030 |
|
290 | 414 | |||||||
X46 | 0.26 | 1.40 | 0.030 | 0.030 |
|
317 | 434 | |||||||
X52 | 0.26 | 1.40 | 0.030 | 0.030 |
|
359 | 455 | |||||||
X56 | 0.26 | 1.40 | 0.030 | 0.030 |
|
386 | 490 | |||||||
X60 | 0.26 | 1.40 | 0.030 | 0.030 |
|
414 | 517 | |||||||
X65 | 0.26 | 1.45 | 0.030 | 0.030 |
|
448 | 531 | |||||||
X70 | 0.26 | 1.65 | 0.030 | 0.030 |
|
483 | 565 |
In addition to its strength, double welded pipe is also able to withstand extreme temperatures, making it suitable for a variety of industrial processes. Whether transporting hot fluids or gases, or operating in environments with fluctuating temperatures, double welded pipe maintains its structural integrity and performance, ensuring reliable operation under even the most challenging conditions.
Additionally, the durability of double welded pipe makes it a cost-effective choice for industrial applications. Their ability to withstand wear, corrosion and other forms of degradation means they require minimal maintenance and replacement, reducing overall operating costs and downtime.
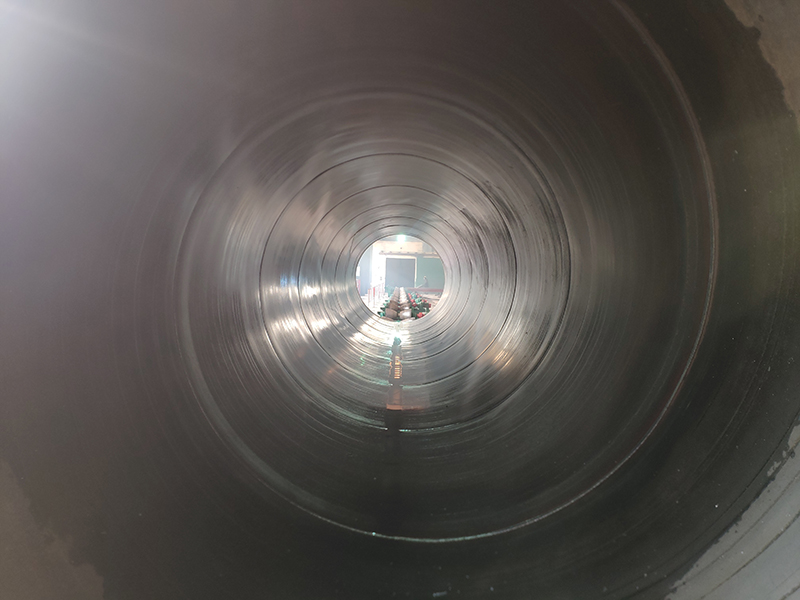
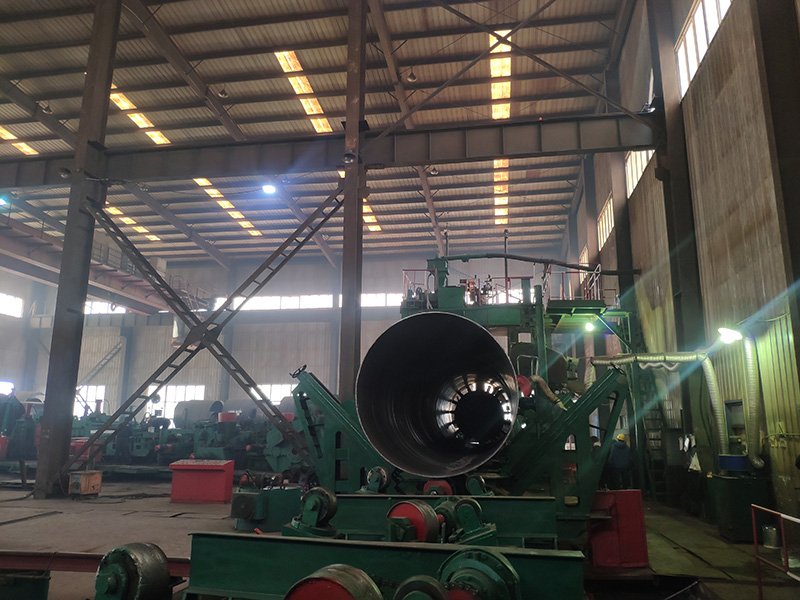
Overall, the use of double welded pipe provides a range of benefits for industrial applications, including strength, durability and reliability. Their ability to handle high pressures, extreme temperatures and harsh environmental conditions makes them ideal for a wide range of industries from oil and gas to chemical processing. With its proven performance and service life record, double welded pipe is a valuable asset to any industrial piping system.
